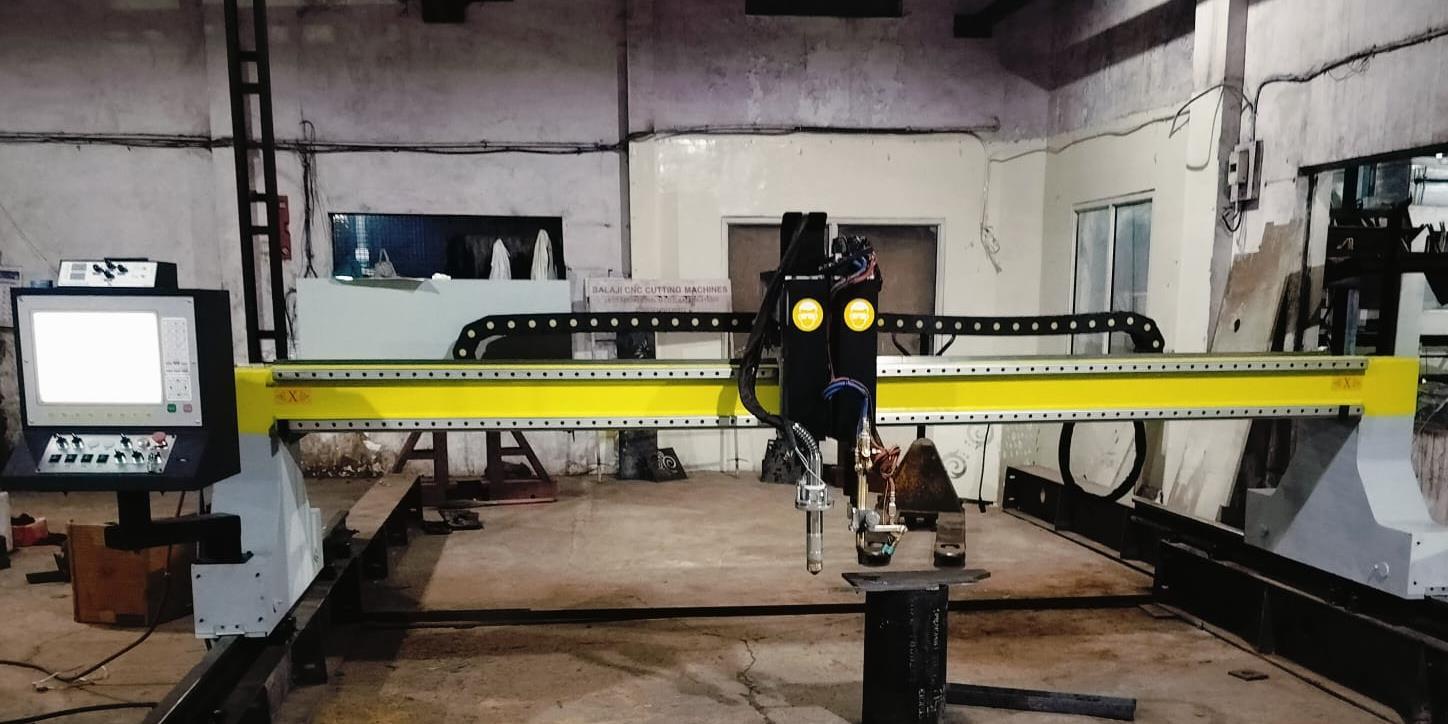
Choosing the Right Cutting Machine: CNC Oxyfuel, Plasma, or Laser?
January 19, 2024
Deciding on the most suitable CNC cutting machine is crucial for industries relying on metal cutting processes. This guide explores three popular methods—CNC oxyfuel, plasma, and laser cutting—providing insights into their advantages, limitations, and applications.
Advantages:
- Suitability for Thickness: CNC oxyfuel excels in cutting thick metal sheets, typically above 1 inch, making it ideal for heavy structural applications.
- Cost-Effectiveness: It proves cost-effective for large-scale cutting operations, especially on thick materials.
- High Cutting Speeds: Offers high cutting speeds, particularly on thick materials.
Limitations:
- Material Limitation: Limited to ferrous metals, excluding non-ferrous materials.
- Precision: Lower precision compared to plasma and laser cutting methods.
- Heat-Affected Zones: The process produces heat-affected zones that may necessitate additional processing steps.
Applications: CNC oxyfuel cutting is preferred for applications involving heavy structural steel, shipbuilding, and other industries requiring the cutting of thick metal plates.
2. Plasma Cutting:
Advantages:
- Material Versatility: Plasma cutting is versatile, suitable for both ferrous and non-ferrous metals.
- Precision: Provides good precision across a wide range of thicknesses.
- Cutting Speeds: Faster cutting speeds compared to oxyfuel, especially on thinner materials.
Limitations:
- Thickness Limitation: Limited to materials with moderate thickness.
- Consumables: Consumables like nozzles and electrodes need regular replacement.
- Initial Cost: Initial equipment cost may be higher compared to oxyfuel cutting.
Applications: Widely used in industries like automotive, HVAC, and metal fabrication, plasma cutting is especially beneficial for applications requiring precision on various metal thicknesses.
3. Laser Cutting:
Advantages:
- High Precision: Laser cutting offers high precision and accuracy, making it suitable for intricate cuts and fine details.
- Minimal Heat-Affected Zones: The process results in minimal heat-affected zones.
- Material Versatility: Versatile for a wide range of materials.
Limitations:
- Cost: Higher initial equipment cost compared to oxyfuel and plasma cutting.
- Thickness Limitation: Limited to thinner materials compared to other methods.
- Maintenance: Requires regular maintenance and alignment.
Applications: Ideal for applications where precision and fine details are critical, such as in the aerospace industry, electronics manufacturing, and artistic metalwork.
Additional Considerations:
Safety:
- All cutting methods involve safety considerations, including fumes, noise levels, and necessary safety equipment. Emphasize the importance of adherence to safety protocols.
Environmental Impact:
- Discuss the environmental impact of each method, considering emissions, energy consumption, and waste generation.
Software and Programming:
- Highlight the importance of user-friendly CNC systems and ease of programming for complex cuts.
Integration with CAD/CAM Systems:
- Discuss how well each cutting method integrates with CAD/CAM systems, streamlining the design-to-cutting process.
Maintenance Requirements:
- Provide information on maintenance requirements, including frequency, potential downtime, and overall maintenance costs.
Future Technological Advancements:
- Briefly mention emerging technologies or advancements in CNC cutting that users might want to watch for, such as improvements in automation and artificial intelligence.
Case Studies or Testimonials:
- Include real-world examples or case studies showcasing the success of each cutting method in specific industries.
Material Waste and Efficiency:
- Discuss material efficiency and waste generation associated with each method, highlighting potential cost savings.
Training and Skill Requirements:
- Highlight the training and skill levels required for operating and maintaining each cutting machine.
Regulatory Compliance:
- Address any regulatory compliance issues related to emissions, safety standards, or industry-specific regulations.
Conclusion:
The choice between CNC oxyfuel, plasma, and laser cutting machines ultimately depends on the specific requirements of the application. If you need high-speed cutting on thick materials with cost-effectiveness in mind, CNC oxyfuel may be the right choice. Plasma cutting offers versatility across different materials and thicknesses. For precision, intricate cuts, and a broad range of material compatibility, laser cutting stands out. Consider factors such as material type, thickness, budget, and required precision when making your decision, and consult with experts in the field to determine the best fit for your specific needs.
You Might Like Also
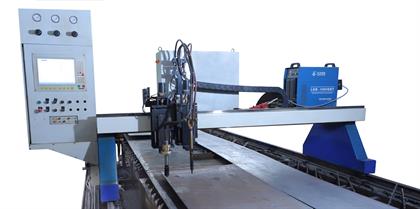
The Cutting Edge: Unveiling the Precision and Power of CNC Oxyfuel Cutting Machines
In the realm of metal fabrication, the CNC Oxyfuel Cutting Machine stands tall as a powerhouse, combining technology and thermal precision to redefine the cutting process. This blog delves into the capabilities, applications, and advancements in CNC Oxyfuel Cutting technology, showcasing its crucial role in shaping the landscape of metalworking. Read More