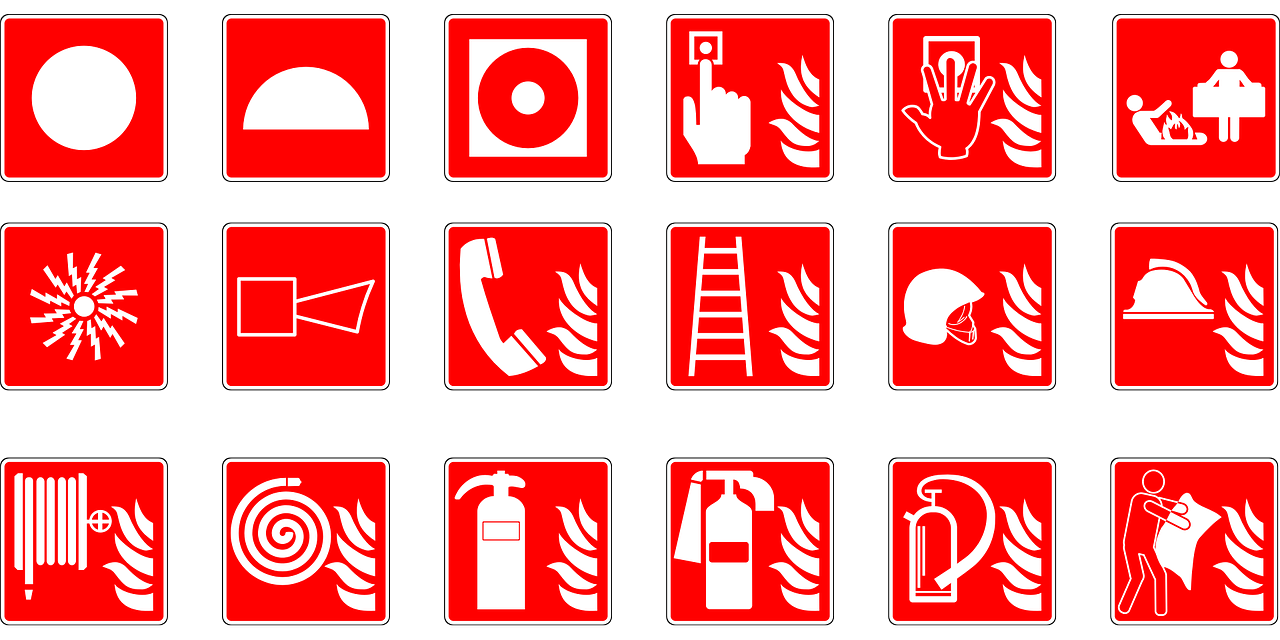
Manufacturing employee safety is vital for the well-being of the individual and the successful operation of the business. Therefore, in an area where heavy machinery, complex operations, and possibly hazardous substances are being used, safety must be monitored and brought into effect. Such companies should have thorough safety practices to maintain safe and productive workspace. Here are five broad guidelines to ensure high-quality manufacturing while prioritizing employee safety:
Regular Training and Safety Education
A well-budgeted training program about safe working practices is the pillar of a sound manufacturing environment. OSHA standards dictate what should be trained to employees, and it is much better if these trainings are done regularly so that the workers will understand better the implications of these safety guidelines as well as preparedness for an incident. Safety education should not be a one-time event but an ongoing process. Train employees on the proper use of personal protective equipment, machine operating procedures, and actions in emergencies. Conduct periodic refresher courses to remind staff of these essential practices and introduce new risks or safety protocols that could occur in the workplace.
Implement Clear Safety Procedures
Clear and well-documented safety procedures are a must for any manufacturing facility. Employees should have easy access to manuals and guidelines on how to perform tasks safely. From machine operation to chemical handling and emergency responses, these procedures should cover it all. Make safety policies visible in common areas such as break rooms or near hazardous equipment so that employees will continuously be reminded of safety practices. Moreover, it is good to have safety officers or managers who will monitor the adherence to these procedures.
Prioritize Preventive Maintenance
Keeping machines and equipment properly maintained on the shop floor for the safety of workers is an aspect that is seen to be very important. Poor-mannered machines and equipment usually tend to malfunction, thus increasing accident probabilities. Regular preventive maintenance checks have been tremendously helpful, and a proactive move can catch an injury before it could occur to a person. Additionally, investing in efficient remote vibration monitoring services to track equipment performance can help detect early signs of malfunction. This will ensure that machinery operates within safe parameters.
Encourage the Use of Protective Equipment
PPE, that is, personal protective equipment, is one of the most basic yet essential forms of workplace safety in manufacturing. It is the employer’s responsibility to ensure they have the right PPE for the particular job, whether gloves, helmets, ear protection, safety glasses, or steel-toed shoes. It is just as vital to train employees on the importance of using personal protective equipment and ways to avoid injuries. The supervisor should periodically check employees for personal protective equipment use. This ensures the equipment remains in good working condition and item replacements are done seamlessly. This attitude regarding PPE should be promoted throughout the manufacturing industry, which will ultimately reduce the odds of accidents.
Foster a Safety-First Culture
The culture of safety first is headed by leadership, and it transcends the walls of the organization. To demonstrate safe behavior, managers and supervisors must adhere to safety procedures and encourage employees to report unsafe conditions. Anonymity in reporting unsafe conditions also helps collect an injury risk that would otherwise not be captured. Recognition and reward for safe behavior are also some of the initiatives that stress the importance of a safety-first culture in the workplace. Safety-first culture at the workplace is addressed by everyone in the organization, and that is some good work to boost the whole safety level of the organization they are working in.
In conclusion, employee safety is not just about having rules and guidelines in place; safety must also mean actively including all employees in the safety process. This brings accident reduction, makes the employees healthier, and goes on towards productivity and sustainability.
You Might Like Also
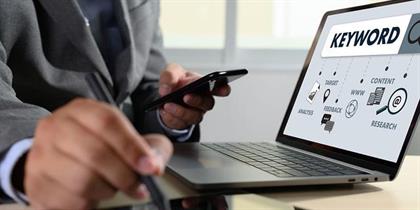
Top SEO Strategies for Dominating Search Engine Rankings in 2025
Search engine optimization (SEO) is the most dynamic aspect of business that makes a company competitive according to the current strategies Read More
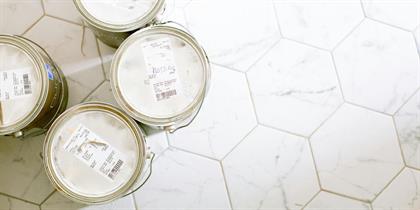
5 Upgrades That Increase Home Values
The kitchen represents one the essential parts of any home. It’s the place where the food is prepared for the whole family Read More
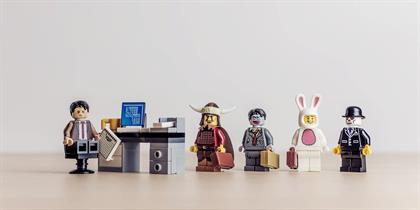
Effective Workforce Management: How to Lead Without Errors
Conducting human resources is a rather complex endeavour, entailing strategic foresight, communication, and decision-making abilities Read More
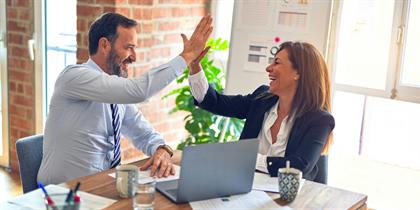
Best Group Health Insurance Companies in India
Health is money, and insurance keeps the money secure! Group health insurance is a smart method for companies to take care of their employees Read More